I want to make a pendant similar to this:
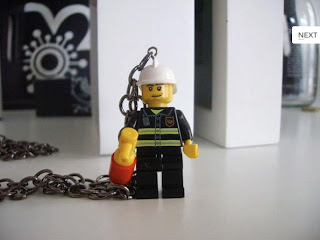
I dont know much about PIM but Im guessing it'd be the way to make them?
So any help on costs/requirements
OR
Any alternative ways to make a plastic mold of an object no bigger than an inch
Welcome to the Newschoolers forums! You may read the forums as a guest, however you must be a registered member to post. Register to become a member today!
heres a paper i wrote the other week on it
Patrick Tice
ME 257 Manufacturing Processes Lab
Dr. John R. Davis
February 22, 2010
Plastic Injection Experiment
Creating a correct plastic part can be very challenging. One process is to heat plastic granules and press them into a mold that contains the shape of the desired part. This is called plastic injection molding. It is a highly favored process due to the short time required to produce the part, the capability of using different plastics, and the preciseness of the desired part.
A group of students recently did a test to determine how different types of plastics are preferred for different parts using plastic injection molding. They used two types of plastic, polystyrene and polypropylene. They determined the difference between them by molding them both into a screwdriver handle, and a checker piece. The molds differed due to the fact that the screwdriver handle has a large cavity and is designed to hold up to pounding, plying and wear and tear. The checker piece however, has a small cavity with many fine lines. The checker piece will not see abnormal wear and tear in its life so the physical properties are not critical.
The students produced several parts using the plastic injection process. This included, loading little plastic granules into the injection machines hopper. The machines heater was turned on, this melts the granules so they mold together nicely. When the plastic was warm, a button was pressed that turned on the air compressor and injected the plastic into the mold. The mold was then separated to reveal the cooling part. Due to the differences in the plastics, the students had to perform several runs to produce a correct mold. The temperature and pressure had to be at the right level to get the plastic to flow into the cavity.
When molding the checker piece, the students noticed that the polystyrene had difficulty getting into all the little creases. Therefore, they needed to increase the temperature and pressure to produce the desired part. The polypropylene however flowed much easier and was able to produce a correct part under much less heat and pressure. The screwdriver however, was different. The cavity in the mold was much larger and didn’t have any fine lines that the plastic would have trouble molding around. The polystyrene produced a more solid part when the polypropylene caved in towards the middle of the part. Also, when the two were struck by a hammer, the polystyrene absorbed the blow and did not break. The polypropylene screwdriver however, fractured and broke apart.
The students deducted from their results that polystyrene is the optimal choice for producing a part that needs to not give in to wear and tear and has a mold that has a large, simple cavity. This is because the polystyrene is a thicker plastic that requires more pressure and a higher heat to fill into the small cavities. The polypropylene has a higher fluidity and is able to form inside small cracks under lower temperature and pressure. This makes it the right plastic for small, intricate parts that do not need a high stress rating.
Plastic injection molding is a common procedure to produce a plastic part. It is capable of using different types of plastic. This has its advantages because different plastics have different qualities. Plastic injection is an effective process to produce a plastic part efficiently and quickly.
Polypropylene screwdriver
Temp (F)
Pressure (PSI)
Result (students rating)
500
40
1/10
500
40
8/10
500
55
8/10
500
60
10/10
500
60
10/10
500
60
10/10
Polypropylene checker piece
Temp (F)
Pressure (PSI)
Result (students rating)
500
50
10/10
500
40
10/10
500
30
5/10
500
37
8/10