I didn’t want to half ass it, and while my skis are definitely not perfect, I think they came out pretty damn good and can only get better from here. So far I have made 52 pairs of prototypes and hope to get more out this year, but that all depends on funding.
Anyway, now to all the photos.
Painting the ski for the ski press. Thanks to Gabe (Jumper Bones) for the help getting all the steel to my house.

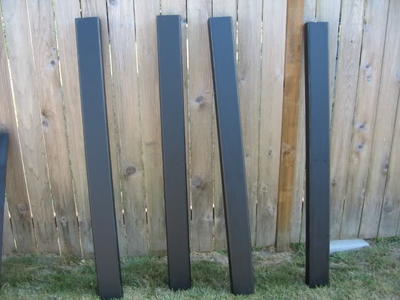
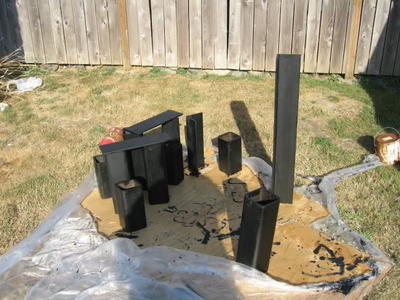
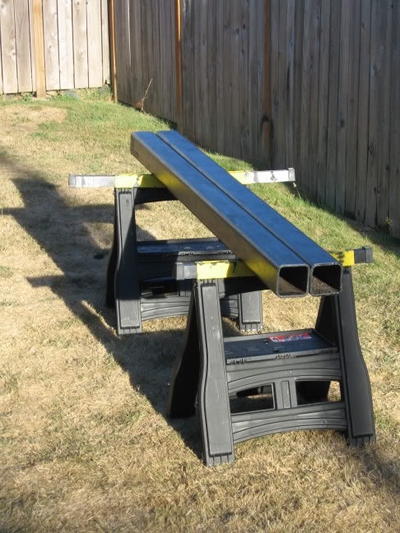
From here, I had to drill the steel. This was…..an interesting process for me. Steel was ½” steel, and all the holes I drilled were ½” wide, so when all was said and done, I had drilled some ridiculous amount like 15 feet of steel.
The hard thing was to make sure everything fit together well. It took me some time to figure out how to get everything drilled correctly, along with the difficult task of moving and drill beams that were almost 300 lbs each, sometimes right next to each other. But when all was said and done (after a lot of drilling), it was all worth it.
I used grade 8 bolts, lock nuts, and at least 2 nuts (sometimes 3) one each of the 148+ bolts that hold the press together. I will be building a new press soon that will be welded, so the time to build it will pale in comparison….anyway, press construction.

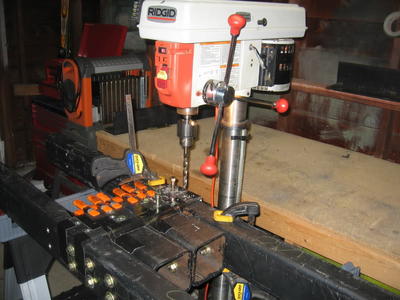
Legs coming together
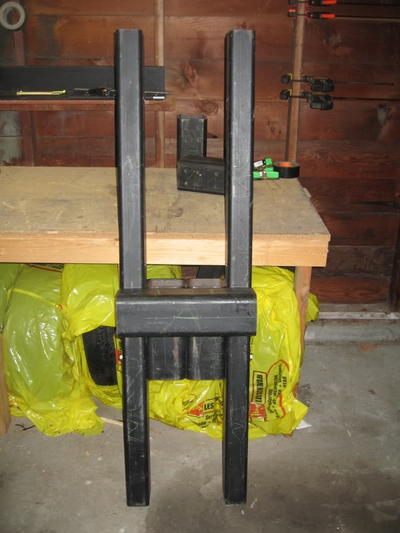




From here, we finally had the moment of truth. Will everything fir together? The press was basically 3 parts; a main press cavity and two leg sections. When it was all said and done, I was so stoked that it turned out.



Best toll EVER for getting the legs on




Press finally came together, and looked great.


So then I moved from the house this idea started out to a new house. Located was great because it was with a few blocks of 10 bars….BUT shop wise, conditions were tight. The shop was 13’ x 17’ and had only 2 110V lines. Ek. But I made due, and had to build it up a lot.
Lots of work to go

So now I had to go and make the best of the space I had. So I build up the shop from the ground up.











When the shop was finally done, I was pretty sure even with the less than 300 square feet I had, I could get everything in there and get this all done.
Go tools







After I made the base mold, I had my rocker sections cnc’ed. I wanted to have the ability to easily swap between different rocker sections, so I designed 3 different rockers, between 15 and 35cm that were easily interchangeable.

I then got the cat track cut, top and bottom molds finished, and put the press together.

I use a planer crib to make my cores. I made an adjustable crib that was not perfect, but it works to do almost 110 cores with 9 different core profiles…










Anyway, first ski out of the press was meh. I don’t really know how it happened, but all of a sudden I knew was that suddenly I laying up a ski scared shitless wondering what I was doing. Very very similar to your first time having sex if I remember to my teenage years correctly.


I used WAY too much epoxy.





Cat approve

Next to the FFFs

Next ski came out better.


After getting 2 skis under my belt, I pressed the first pair I would get to ski on.



Skied them up a crystal. Several other people got to use them and everyone seemed to like them.



Git ir done

Buddy david took them out too

Anyway, kept on working and got a few more pairs out. Here is the girlfriend showing off Wren’s wrenegades.


Then things picked up a lot. I stated off expecting to make 7 pairs of skis at first. Well at the end we had produced 52 pairs.

VDS

Cutting jig

Tipspacers

Base material

Fiberglass broken up by size

Some cores


Rest of cores

From here on I could show a ridiculous amount of photos, but I will just throw a handful up.
At the end I had a lot of help from friends just helping me get the skis done. First and foremost, Sam Caylor. His is the man and he cut and finished a ton of skis.
Also David, Billy, Rowen, Will, and Josh all showed up to help get the skis done.
Will with his skis












One of the things that was the hardest part for me was hand cutting the edge notch of the ski. Sometimes I did a good job, other times not as well.
Before

After



Zoe’s custom pair vs. a pair of caylors







Where I lived there was 10+ ally cats. They are great company



Marshal’s Great Scotts getting layed up

Wood veneer










Anyway, that is obviously a lot of photos.
When all was said and done I had made 52 different skis.


